Der Ironman für Photovoltaikmodule findet täglich in unserem hauseigenen Qualitätslabor statt. Denn es gilt: Nur die Besten werden IBC SOLAR-Module! Um dieses Prädikat zu erhalten, müssen die Module eine Reihe von Härtetests bestehen, angefangen bei Klimakammer und Flasher, über einen Feuchtetest bis hin zu Langzeitbeobachtungen auf unserer Testanlage. Als ersten Beitrag der Serie stellen wir unsere neueste Anschaffung, den Belastungstisch, vor.
Die mechanisch-statische Belastungsprüfung nach DIN EN 61215-2:2017 ist unser neuestes hauseigenes Prüfverfahren. Hier wird das Photovoltaikmodul sechs Stunden lang höchsten Belastungen ausgesetzt. 12 Prüfzylinder mit Vakuumsaugern simulieren bis zu 5.400 Pascal Druck- und Zugkräfte – drei Stunden auf der Vorderseite, drei Stunden auf der Rückseite. Dabei wird das Modul kräftig gebogen. Um den Belastungstest zu bestehen, darf der Testling hinterher keine Verformungen, Ausbrüche, Ablösungen, Mikrorisse oder Leistungsverluste aufweisen. Dieses Verfahren müssen alle Module, die wir in unserem Portfolio anbieten, regelmäßig durchlaufen.
Die Eigenmarke muss noch mehr aushalten
Zur Qualitätssicherung unserer Eigenmarke IBC SOLAR Line gehen wir noch einen Schritt weiter. Unsere eigenen Module müssen zusätzlich eine dynamische Belastungsprüfung bestehen. Hier wird mit einem Hochfrequenz-Test ein „Flattern“ simuliert, also eine Belastung, wie sie beispielsweise bei Stürmen über mehrere Stunden hinweg auf die Module einwirkt. In der Praxis nehmen seit einigen Jahren aufgrund des Klimawandels solche massiven Windbelastungen bei Extremwetterlagen zu.
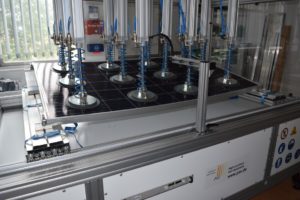
Gemeinsamer Test für mehr Praxisnähe
Das ist aber noch nicht alles, was der Belastungstisch kann. Der eigentliche Clou ist der gemeinsame Test von Modul und Halterungssystem. Denn um den Test möglichst realitätsnah zu gestalten, werden die Module zusammen mit Montagesystemen getestet. Damit die Installation auf schrägen Dächern simuliert wird, sind Neigungen möglich und alle Komponenten des Montagesystems können auch einzeln geprüft werden. Warum das wichtig ist? In der Praxis kommt es auf das Zusammenspiel zwischen Halterung und Modul und damit auf die Systemstabilität an. Und die ist entscheidend für die Widerstandsfähigkeit und Langlebigkeit eines PV-Systems.
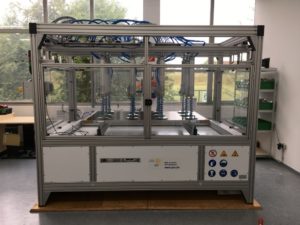
Schnellere Reaktion auf Veränderungen am Markt
Das neue Belastungstestverfahren eröffnet uns die Möglichkeit, schneller auf Produktveränderungen seitens der Hersteller zu reagieren. Ein Beispiel dafür sind abnehmende Rahmenhöhen, die nicht nur Auswirkungen auf die Stabilität des Moduls haben können, sondern auch das Zusammenspiel von Modul und Montagesystem beeinflussen. Für uns steht hier die Überprüfung und dauerhafte Sicherung der Systemqualität im Vordergrund. Ein weiterer Punkt ist das Auslaufen des Mindestimportpreises (MIP) für chinesische Photovoltaikmodule. Wir wollen weiterhin sicherstellen, dass unsere Kunden ausschließlich Qualitätsware erhalten, deren Garantien halten, was sie versprechen. Und deshalb sagen wir: Vertrauen ist gut. Aber Kontrolle ist besser!
Hier ist der Belastungstest im Video (YouTube) zu sehen.
Wir benötigen Ihre Zustimmung, um Inhalte von YouTube zu laden.
Im nächsten Beitrag Stellen wir die Temperaturwechselprüfung in der Klimakammer vor.